Today, Xiamen Birtley will take you to gain a deep understanding of the detailed process of making paper packaging boxes and enjoy this magical craft journey together.
1.Design phase: This is the beginning of the entire process, and the designers will carefully conceive the shape, size, and style of the box to perfectly match the characteristics and needs of the product.
2.Material selection link: In order to ensure the quality of the packaging box, we need to select high-quality paper. These papers have sufficient strength and toughness to withstand the challenges of packaging and transportation.
Generally, ordinary color boxes are basically made of 300G to 400G copper paper, gold and silver cardboard, and special paper can also be used for special requirements. The inside of the gift box is gray cardboard and the outside is decorated with colored paper or special paper. Color paper is made of double copper and dumb copper paper. Some of them use 80G, 105G, 128G, 157G. These gram-weight papers are more commonly used. The outer mounting colored paper of gift boxes rarely uses more than 200G; because the colored paper is too thick to mount on the gift box, it is easy to foam and the appearance looks not very good. Design the outer packaging according to the product, and then choose the paper quality and craftsmanship.
3. Precise cutting: Use advanced cutting equipment to precisely cut the paper into the required shape and size to ensure that every part matches perfectly.
4. Folding and bonding: This is a key step that requires skill and patience. Fold carefully according to the design requirements, and then use the appropriate adhesive to bond each part firmly together.
5.Decoration and processing: In order to make the packaging box more attractive, various decorative and processing operations can be carried out, such as printing exquisite patterns, gilding, embossing, etc., giving the box a unique visual effect.
Most of the gift boxes are made of printed paper, and the gift box is an outer packaging box, which pays attention to the printing process. The most taboo color difference, ink dots, and rotten boards will affect the aesthetics.
① Laminating: Laminating a layer of transparent plastic film on paper products is called laminating. Laminating film is divided into "light film" and "dumb film". The surface effect of the light film is crystal clear and bright, changing and colorful, and not changing color for a long time. With soft hand feeling and colorful surface design, it is a safe and environmentally friendly building material that can be selected according to the changes in color perception of the times. The color of the matte film can be seen to be a foggy surface, and the matte matte surface is matte after coating.
②Foil stamping: Hot stamping is to heat the metal printing plate, apply foil, and emboss golden characters or patterns on the printed matter.
③Silver hot stamping: The process principle is basically the same as that of hot stamping, except that the materials used for the two are somewhat different. In appearance: one has a golden luster and the other has a silver luster.
④UV: UV refers to UV coating, that is, Ultraviolet coating (ULTRAVIOLET), which uses ultraviolet radiation to trigger an instant photochemical reaction of UV coating, forming a bright coating with a network-like chemical structure on the surface of the printed matter.
⑤Pressing concave and convex: It is a printing method that does not use ink. It is to place the packaging box in a set of intaglio and relief plates corresponding to the pictures and texts. Under a certain pressure, the two templates are pressed against each other to make the packaging box present a relief-like concave-convex image The process of text and pattern.
6.Quality inspection: At every stage of the production process, strict quality inspections must be carried out. Ensure that the structure of the box is strong, the appearance is perfect, and there are no defects.
7. Pack and ship: Products can be packed in 3-layer or 5-layer corrugated boxes, transported over long distances and then wrapped with a woven tape to prevent damage to the carton during transportation and thus damage to the product.
The entire production process of the paper packaging box is full of fine craftsmanship and attention to details. Every step is crucial and jointly creates high-quality packaging boxes.
This process not only showcases human wisdom and creativity, but also adds a touch of beauty and practicality to our lives.
If you have more interest or questions about the production of paper packaging boxes, you are welcome to communicate with us at any time.
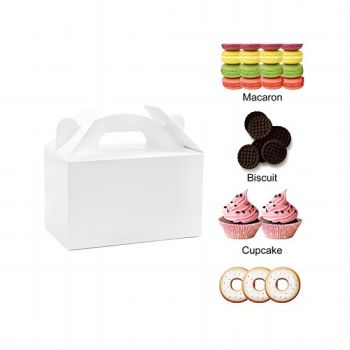
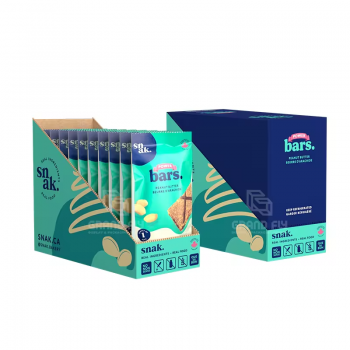
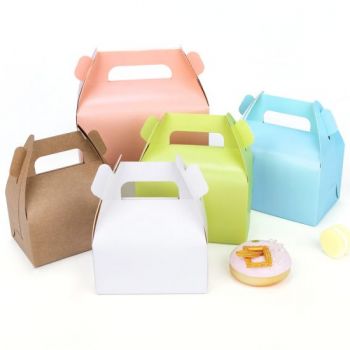
BDL Portable Carton West Point Cake packing paper box
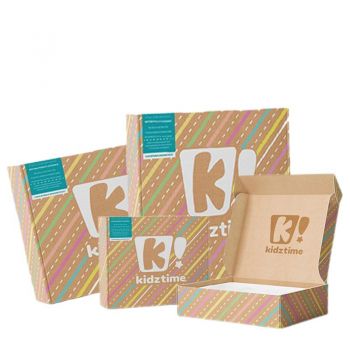
BDL Aircraft Box Customized Natural Corrugated Paper Packaging Box
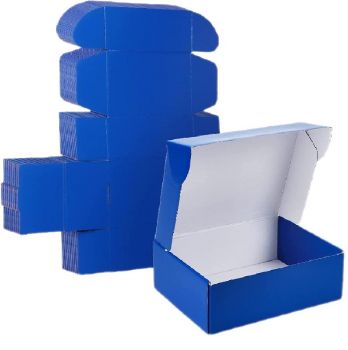
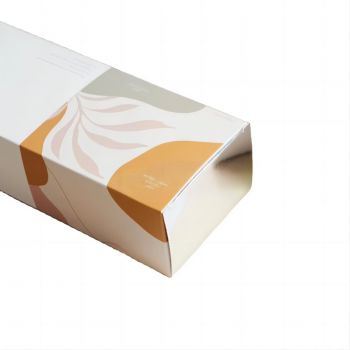
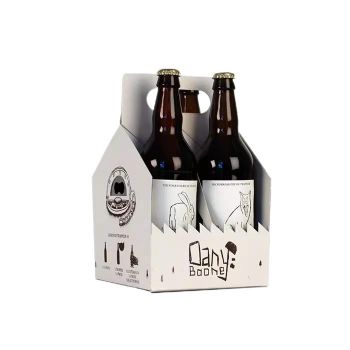
BDL Hot New Best Selling Beer Paper Corrugated 4 Pack Bottle Carrier
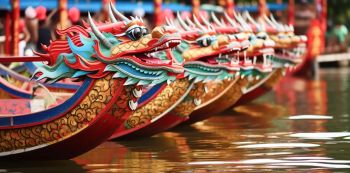
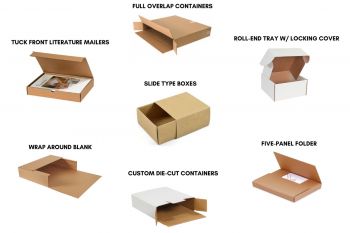

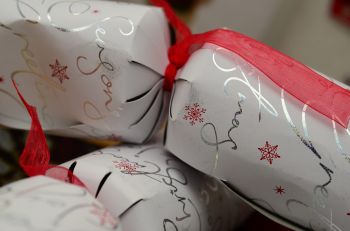